In other articles, we discussed topics such as "What is copper loss?" and "What is the core power material?" which covered knowledge related to the core. In this article, we will focus on how different appearances of the core can have various impacts on the design, providing a detailed explanation.
*The iron core mentioned in the following content refers to the collective term for ferrite magnetic cores.
1、How does the difference in the appearance of the iron core affect ?
The shape of the iron core directly affects the specifications and characteristics of the electrical appliance.
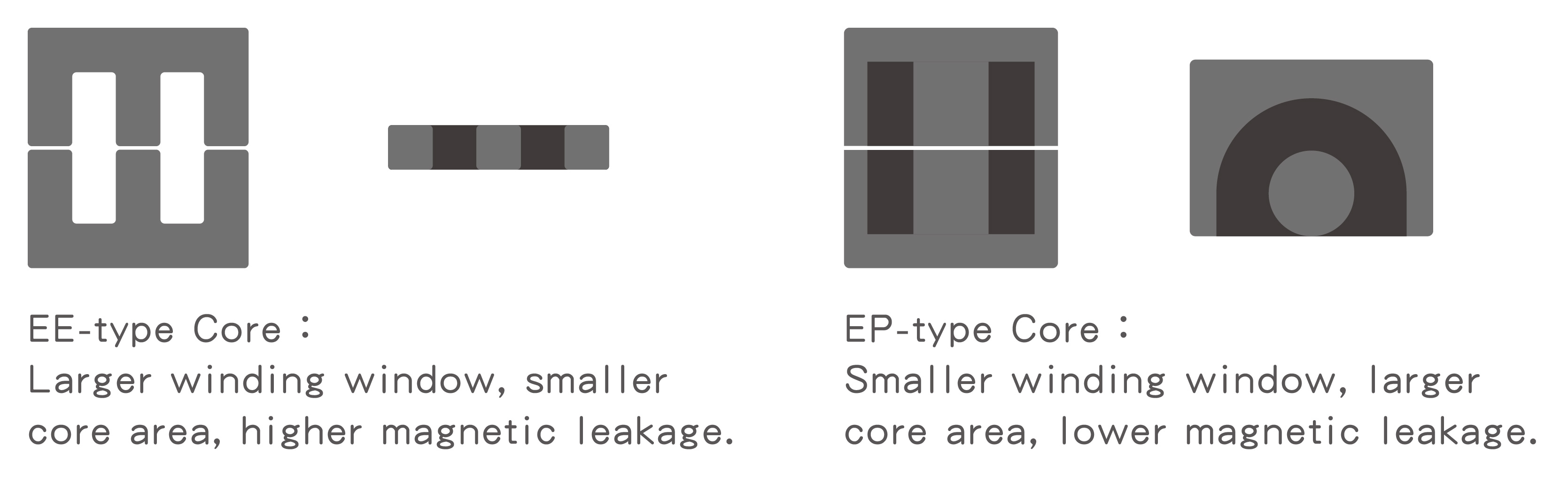
1.1 Impact of Core Size and Shape on Winding Window :
• As the core size increases, the area of the winding window also increases. This is because the increased width of the core leads to an increase in its circumference, resulting in a larger winding window area.
• Even when two different shapes of cores have the same width, their winding window structures will differ due to their distinct shapes. Therefore, the size of the winding window will affect the diameter and number of turns of the winding wire.
• Smaller winding window areas will result in smaller diameters and turn numbers of the winding wire. This will lead to a decreased current-carrying capacity of the wire, while increasing copper losses, resulting in more copper losses.
• Larger winding window core shapes will increase the occurrence of magnetic leakage and reduce EMI (Electromagnetic Interference) effectiveness. This is because larger core shapes may cause more magnetic leakage.
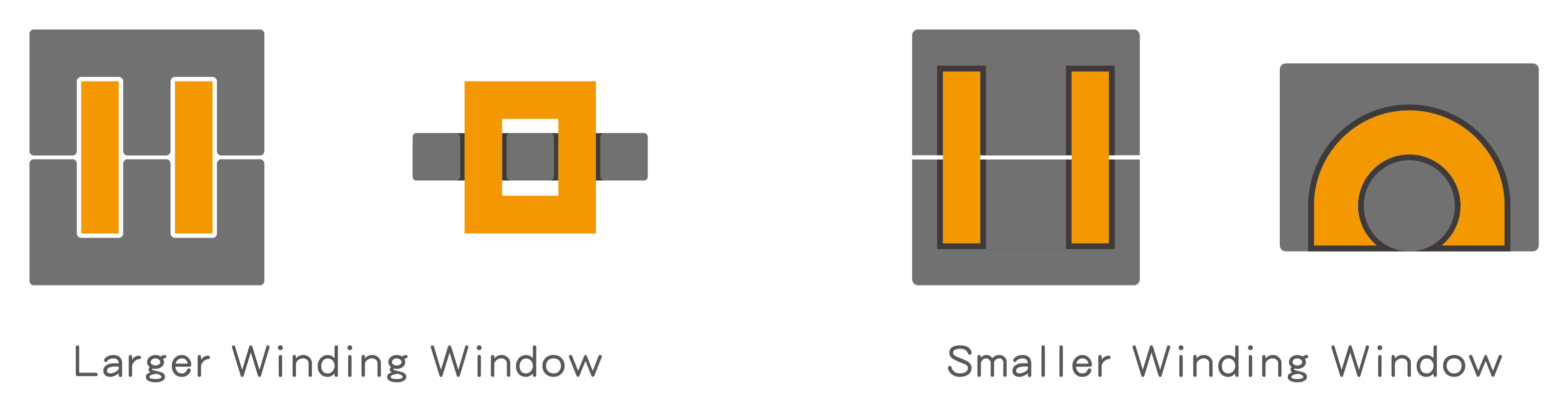
1.2 Impact of Core Size and Core Area :
• As the core size increases, the core area also increases. This is because the width of the core increases, leading to a larger core area.
• Even when two different shapes of cores have the same width, their core structural areas will differ due to their distinct shapes. Therefore, the size of the core area will affect its AE value (effective cross-sectional area). A higher AE value indicates a higher permeability of the core, resulting in higher inductance when the number of turns is the same. Consequently, when the core area becomes larger and the winding window area decreases, the wire diameter used in the winding will become smaller, reducing its current-carrying capacity and increasing copper losses.
• Larger core areas may reduce magnetic leakage and enhance EMI (Electromagnetic Interference) effects. A larger core area can effectively concentrate the magnetic field within the core, thus reducing magnetic leakage. At the same time, since EMI is often related to changes in the electromagnetic field, a larger core area may strengthen the EMI effect.
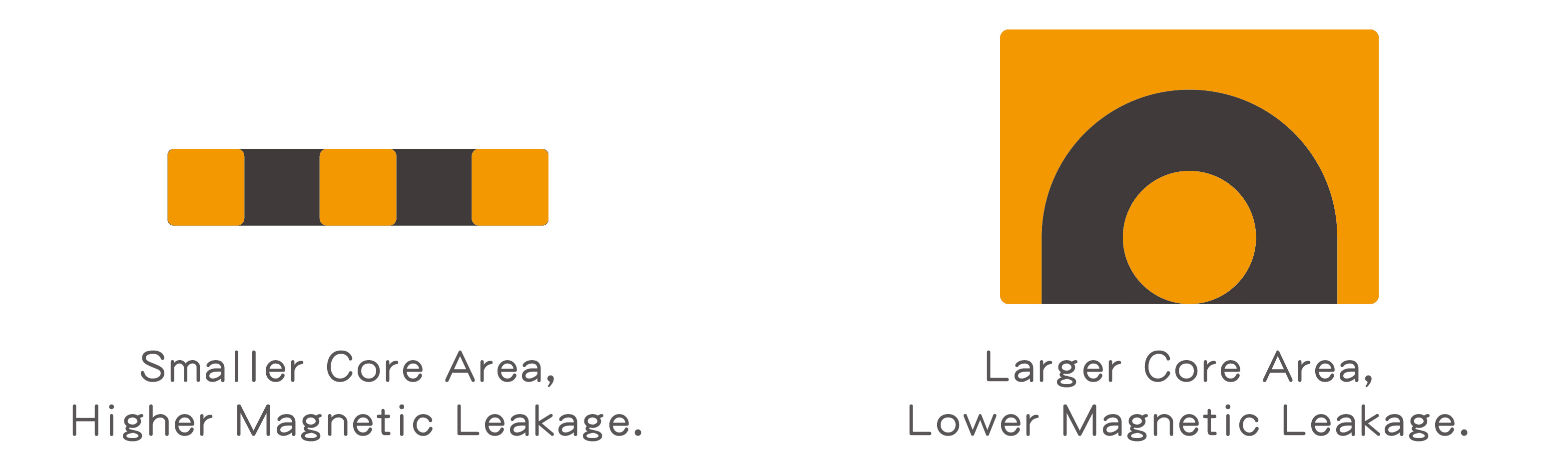
1.3 Differences between Closed-core and Open-core Iron Cores:
▶
Closed-core transformer :
1. Fully enclosed structure: The structure of the closed-core iron core is fully enclosed, and the magnetic field circulates within the core without leaking to the outside. This reduces magnetic leakage and improves the efficiency of the equipment.
2. Higher efficiency: Due to the elimination of most magnetic leakage, devices using closed-core iron cores generally have higher efficiency.
3. More complex winding: The design of the closed-core iron core requires more and complex winding. Because of the closed structure, copper wires need to be wound in narrow spaces with multiple layers or multiple wires, using layering techniques to isolate different layers of winding.
4. Higher cost: The labor cost for closed-core iron cores is usually higher due to the more complex winding and structural design, often relying on manual labor as automated equipment cannot replace human precision.
▶
Open-core transformer :
1. Partially open structure: The open-core iron core has a partially open structure, allowing some magnetic leakage to occur.
2. Lower efficiency: Due to the presence of some magnetic leakage, open-core iron cores typically have lower efficiency than closed-core ones.
3. Simpler winding: The design of the open-core iron core allows for simpler winding since complex multi-layer winding is not required within narrow spaces.
Lower cost: The winding and assembly cost for open-core iron cores is usually lower due to their simpler structure.
4. For applications that require high efficiency and low magnetic leakage, closed-core iron cores may be a better choice, even though they come with higher costs. On the other hand, for applications with less stringent requirements, open-core iron cores may offer a more cost-effective solution. Designers need to carefully consider the specific needs and perform an evaluation when choosing between the two types of iron cores.
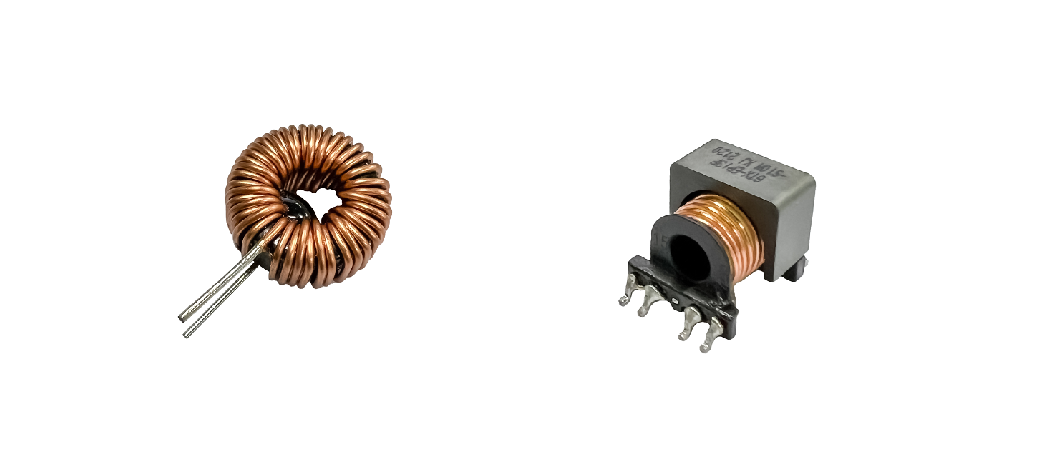
( Closed Winding 、 Open-core transformer )
1.4 The difference between the shape of the column in the iron core: square column and round column
When winding around a square column, the positions of the corners will generate greater stress, which benefits wire winding. However, the wire is more prone to deformation, affecting copper losses and insulation.
Winding on a circular core results in lower stress on the wire corners, making it less suitable for wire winding, but the wire is less likely to deform.
When the cross-sectional area of the core is the same, a circular core will have a shorter winding length compared to a rectangular core.
When considering the overall performance of the electrical appliance, it is important to optimize the appearance of the iron core. The selection of the iron core shape, structure, window area, and core column shape should be based on the specific application requirements. Through simulation and testing, the impact of different parameters on performance can be evaluated, and the optimal design can be determined. Material selection and process optimization should also be considered to further enhance the efficiency, performance, and cost-effectiveness of the iron core. Continuous research and innovation can lead to ongoing optimization of the iron core's appearance and overall system performance.

( Iron core-Square columns 、Iron core- Cylinder )
2、The influence of the iron core on the inductance formula :
It can be seen from the inductance calculation formula that its magnetic permeability, the square of the number of winding turns N, and the equivalent magnetic circuit cross-sectional area Ae are proportional to, and inversely proportional to the equivalent magnetic circuit length le.
Therefore, when the iron core area is fixed, the higher the height, the larger the window, the more the number of turns can be increased, and the greater the inductance value, but the larger the iron core height, the longer the le length, and the smaller the inductance.
3、What are the shapes of iron cores?
1. POT Core :
The appearance is cylindrical, providing excellent iron core encapsulation and EMI shielding effects. The circular central column maintains good copper losses and voltage withstand specifications, and can be secured to the PCB board using screws and nuts.
However, it is not conducive to heat dissipation and wiring, and the space for routing is limited.
( POT Core )
2. RM Core :
The appearance is octagonal, providing a larger exposed space compared to POT-type cores, which is advantageous for heat dissipation and exposed wire leads for wiring. It can be secured using iron clips to ensure proper core assembly. The RM-type core has a higher area utilization efficiency.
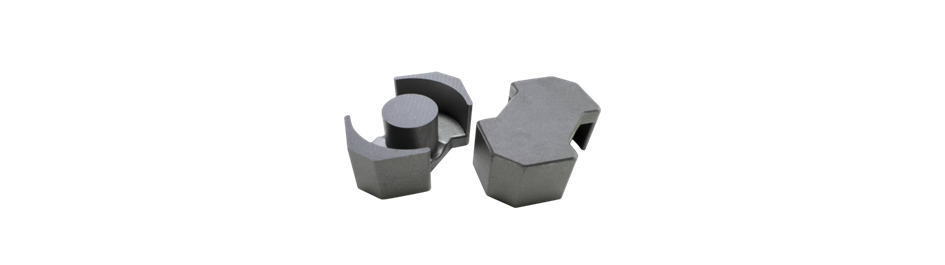
( RM Core )
3. EE Core :
The appearance is rectangular, offering a larger exposed space compared to POT-type cores, making winding and assembly relatively simple. The EE-type core is widely used and can be manufactured in a flat shape. Due to its good heat dissipation performance and the ability to be stacked, it allows for assembly in different orientations. However, its EMI shielding effect is relatively poor.
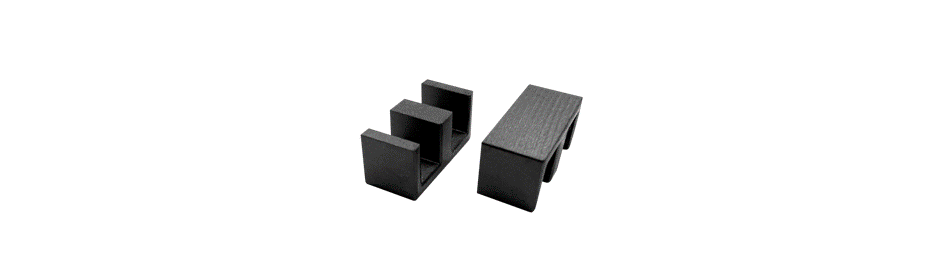
( EE Core )
4. E Core :
It has a rectangular shape, and the E-type core provides sufficient winding space, facilitating heat dissipation and exposed leads for wire winding.
When the cross-sectional area of the columns is the same, the winding length of a circular core is reduced by approximately 11%, resulting in an 11% decrease in copper losses.
( ER、EP、ETD、EFD Cores )
5. PQ and IPQ Cores :
They have a rectangular shape. The PQ core optimizes the ratio between core volume, surface area, and winding area. Some models can be installed and secured using iron clips to ensure core junction. They are widely used in high-frequency and high-power applications.
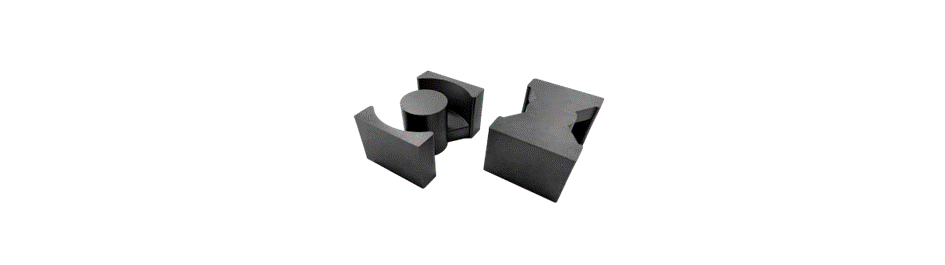
( PQ Cores)
6. EP Core :
With a square appearance, the EP-type core exhibits excellent encapsulation and shielding effects. This unique shape minimizes the influence of air gaps formed at the contact surfaces during core assembly, ensuring optimal space utilization.
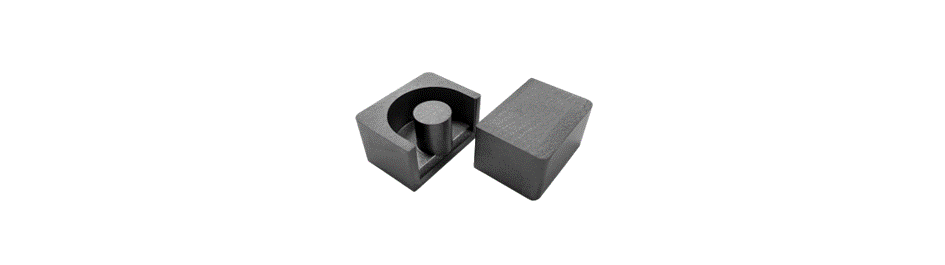
( EP Core )
7. SQ and T Toroidal Cores :
Ring-shaped cores are widely used due to their lower production cost compared to other core shapes. They do not require bobbin or assembly and can be wound using a winding machine. With a closed-loop structure, they have low leakage inductance and provide good EMI performance.
These are some common core shapes, each with its own advantages and application range. Choosing the appropriate core shape can enhance the performance and efficiency of electronic components.
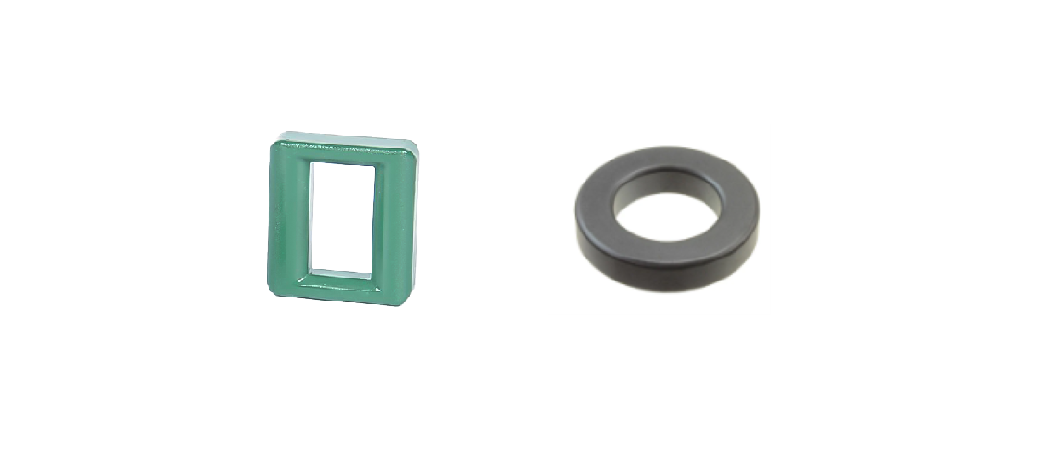
( SQ and T Toroidal Cores)
Related articles :
•
What is copper loss?
•
What is the core power material?
•
What is a high frequency transformer?