Content
1. Power inductor vibration and noise causes
2. Power inductor main body vibration and noise amplification system
3. Various causes and effects of vibration
4. Various reasons for noise amplification
5. Four solutions for power inductance noise
Sometimes when electronic devices in homes or automotive electronics are in operation, a high-pitched noise known as " whistling" can occur. The noise from inductors, which is caused by a multitude of factors and is very complex, can be a nuisance. This article outlines the reasons for the noise in power inductors and offers effective solutions.
1. Power inductor vibration and noise causes
① In the output power mode, factors such as load variations can result in audible frequency vibrations perceived by the human ear. The sound waves generated by the vibration of the inductor propagate as elastic waves in the air, and humans can hear the "sound" within the working frequency range of approximately 20Hz to 20kHz.
During the operation of the power inductor in a DC-DC converter when an alternating current or its pulsating wave within the audible frequency range flows through, the inductor coil will experience slight vibrations due to changes in the load. The resulting sound waves can be heard by the human ear, and this phenomenon is referred to as "coil noise" or sometimes interpreted as a whistling sound (Figure 1).
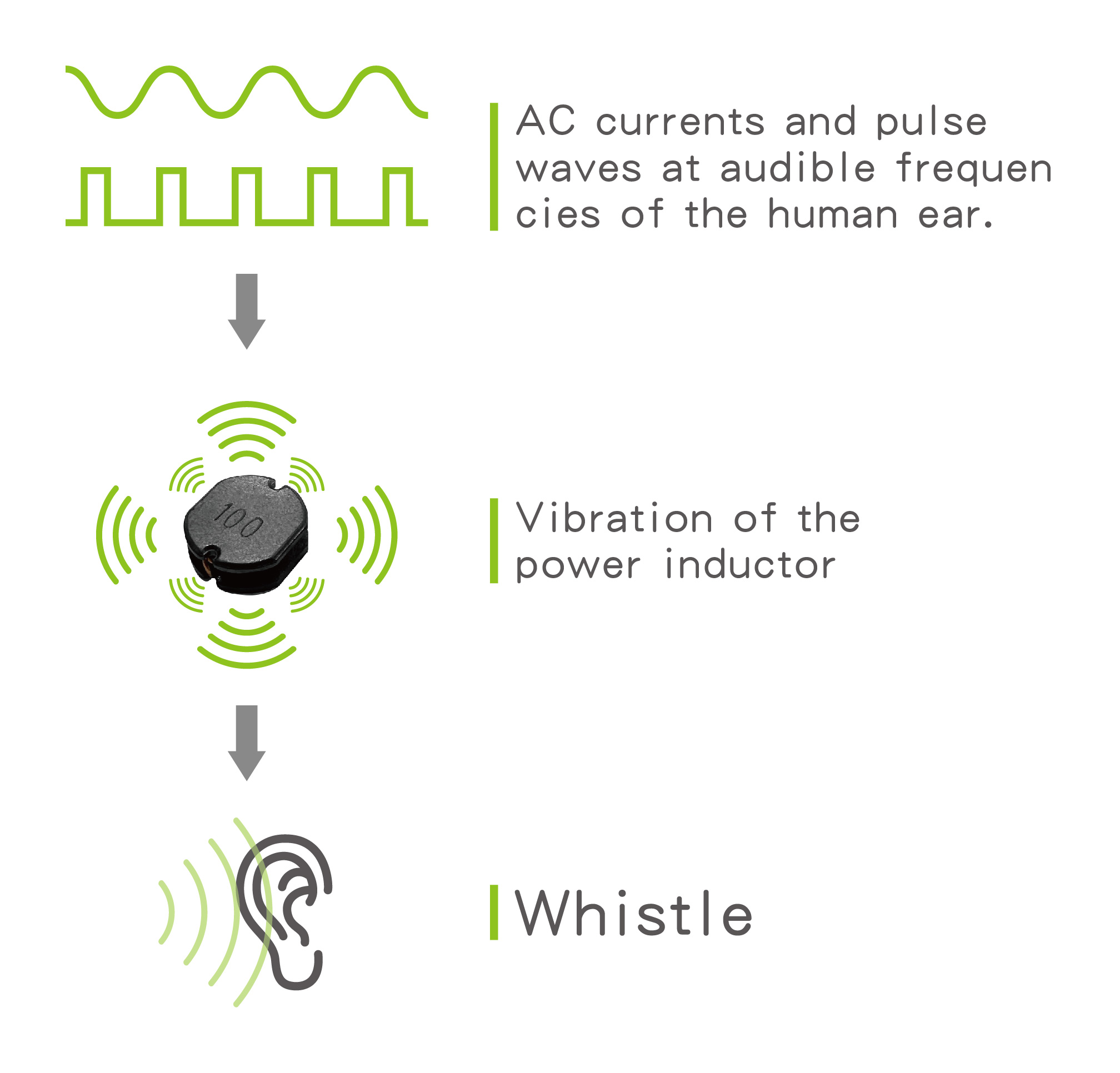
Figure 1: Power Inductor whistling Mechanism
As electronic devices become more advanced, inductors are increasingly being used in electronic devices, and power inductors in DC-DC converters have become one of the sources of noise.
DC-DC power inductors are switched ON/OFF by switch devices, which generates a pulse current. A steady DC current with a constant voltage can be obtained by controlling the length of time the switch is ON (pulse width). This method is called Pulse Width Modulation (PWM) and is widely used as the main method in DC-DC converters.
② Whistling caused by intermittent operation of DC-DC converter, such as PWM dimming
To save energy, the intermittent operation of DC-DC converters has introduced an automatic backlight dimming function for mobile terminal LCD displays. This is software based on the use of scene lighting, which automatically changes the backlight brightness, thereby increasing the battery life. The form of manipulating the LED lighting and off time lengths is called a PWM dimmer. The advantage of a PWM dimming system is that there is less chromaticity variation caused by dimming, and its core is used for the backlighting of notebooks and their tablets.
The PWM dimmer induces intermittent operation of the DC-DC converter at a low frequency of around 200Hz, and adjusts the brightness by repeatedly turning the backlight on and off. In a stable loop of on/off cycles, lengthening the on-time may brighten the display, while shortening it may darken the display. The intermittent operation at around 200Hz is basically imperceptible to the eye in terms of backlight flicker. However, as it is within the audible frequency range for humans, the power inductor mounted on the board may vibrate and cause whistling noise as the intermittent current flows through it.
③ Whistling caused by DC-DC converter
DC-DC converters operating in PWM mode have the characteristic of achieving efficiency levels of 80-90% or higher during normal operation. However, under light loads such as standby conditions, the battery life can be severely reduced. The losses caused by switching are directly proportional to the frequency. As a result, stable switch losses occur under light loads, leading to decreased efficiency.
To address this issue, the PWM method should be automatically replaced with PFM (Pulse Frequency Modulation) mode for DC-DC converters operating under light loads. PFM mode involves controlling the switch frequency with a fixed ON time, providing load relief.
Since the ON-time is stable, the switch frequency may gradually decrease as the OFF-time increases. Switch losses are proportional to the frequency, so the frequency can be reduced under light loads. However, the reduced frequency may fall into the audible range of 20 Hz -20KHz, causing the power inductor to generate whistling noise.
④ Whistling caused by load
To save battery power, various power-saving technologies are employed in mobile devices such as laptops, which can lead to whistling from inductors. For example, the CPU in a laptop has a periodic variation in its power consumption due to low power and its processing capability. When this cycle falls within the audible frequency range, power inductors may whistling due to the effect.
2. Power inductor main body vibration and noise amplification system.
When the current flows through the audible frequency range of the human ear, the vibration of the power inductor body will cause whistling.
The reasons for its vibration and noise may be as follows
【Cause of vibration】:
➀ Ferrite core magnetization leads to mutual attraction
➁ The efficacy of magnetostrictive (magnetic strain) ferrite cores
➂ Winding vibration caused by magnetic leakage
【Causes of noise amplification】 :
➀ Leakage flux causes an effect on the surrounding ferrite
➁ Contact with other components
➂ Consistent with the number of natural vibrations of the entire component including the substrate (The causes of vibration that cause the whistling of the power inductor and the causes of noise expansion are summarized in Figure 2.)
The main contents of these reasons are explained below.
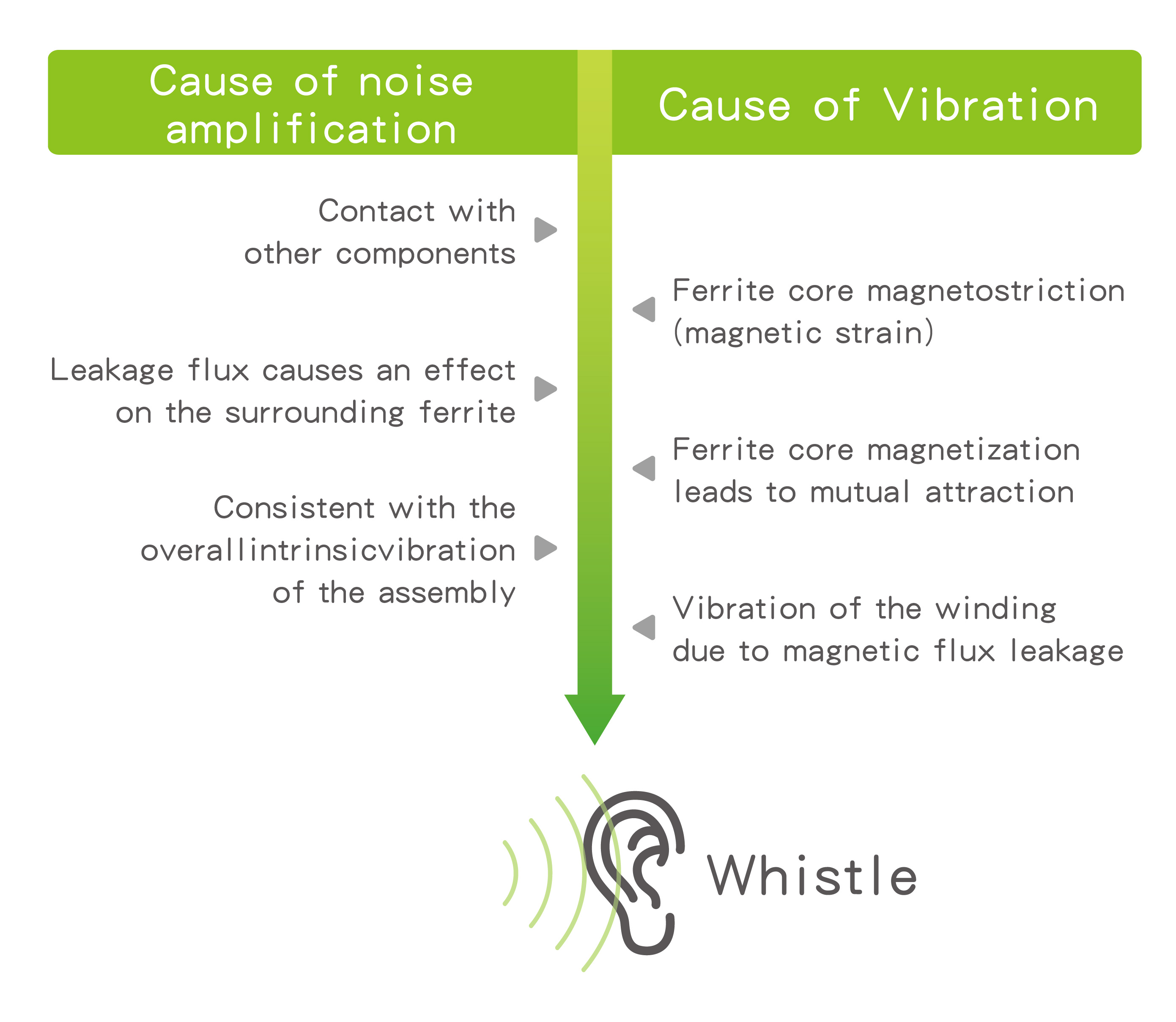
Figure 2 : Causes of whistling and amplification of acoustic noise of power inductors
3. Various causes and effects of vibration
Cause of Vibration ➀ : Magnetostrictive Effect of Ferrite Core
After magnetizing a ferrite core with a magnetic field, its shape undergoes slight changes. This phenomenon is known as "magnetostriction" or "magnetic strain." In inductors with magnetic cores such as ferrite, the alternating magnetic field generated by the winding causes the ferrite core to expand, sometimes resulting in detectable vibration sound.
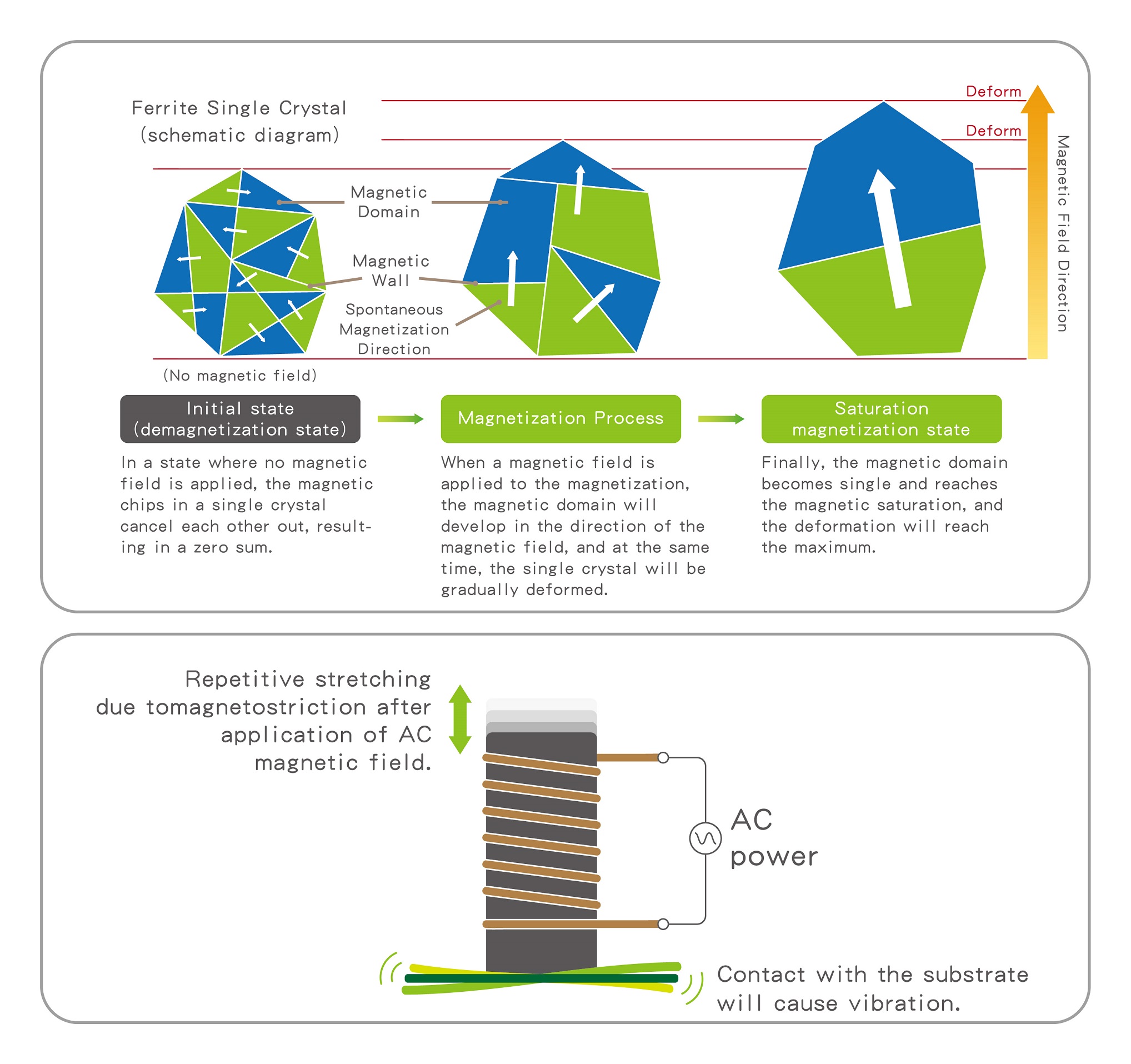
Figure 3: Ferrite magnetostriction (magnetic strain)
In the magnetic domain, the atomic magnetic moments are oriented in the same direction, so the magnetic domain is a spontaneously magnetized micro-magnet with a constant orientation, but ferrite generally does not exhibit magnetic characteristics of a magnet. This is because the arrangement of multiple magnetic domains in ferrite causes spontaneous magnetization to cancel each other out, resulting in a demagnetized state on the surface.
During the magnetization process, subtle positional changes can occur at the atomic level, which manifest as magnetostriction at the macroscopic level, resulting in a visible change in the appearance of the ferrite.
The appearance changes caused by magnetostriction are extremely subtle, on the order of one ten-thousandth to one millionth of the original size. However, as shown in Figure 3, when an alternating magnetic field is applied, the ferrite core may undergo repeated expansion and generate vibrations.
Therefore, the vibration of the ferrite core caused by magnetostriction cannot be completely eliminated in power inductors. Although the level of vibration in a single power inductor is small, when it is mounted on a substrate, if the vibration matches the natural frequency of the substrate, the vibration can be amplified, resulting in audible whistling.
Vibration Cause ➁ : Mutual Attraction Caused by Magnetization of Ferrite Magnetic Core
When a ferrite is magnetized by an external magnetic field, it exhibits magnetic properties and attracts surrounding ferrite. As shown in Figure 4, this is an example of a fully shielded power inductor. It is a power inductor with a closed magnetic circuit structure, but there is a gap between the E-shaped core and the shield ring, and noise sometimes emanates from this gap.
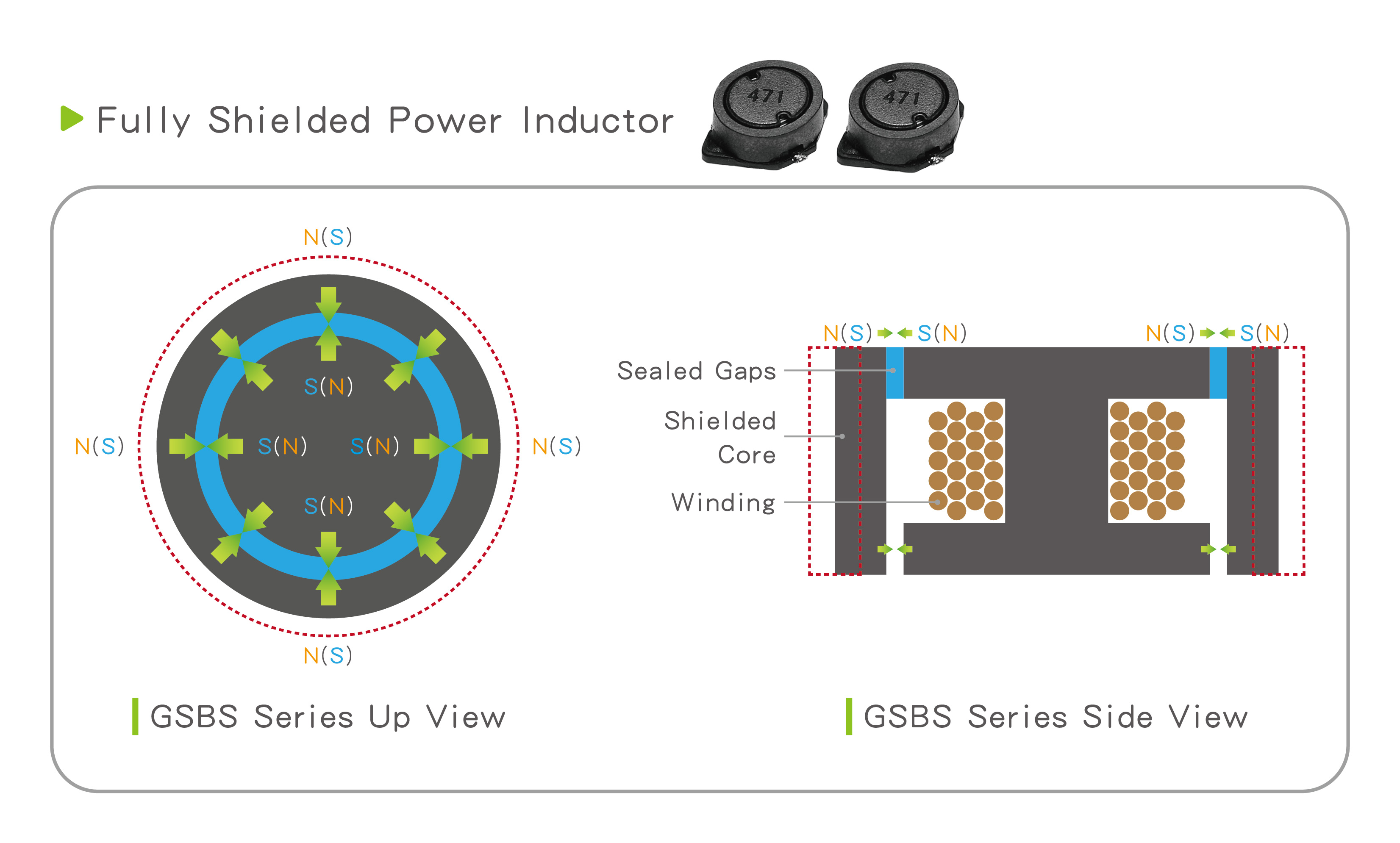
Figure 4: Drum cores and shield ring attract each other, resulting in whistling
When an alternating current flows through the winding, the magnetized drum core and shield ring may attract each other due to their magnetism. If the vibration occurs within the audible frequency range, noise can be heard. The gap between the drum core and the shield ring is closed by an adhesive, but a hard material cannot be used to avoid stress cracking, and the vibration caused by mutual attraction cannot be completely suppressed.
Vibration Cause ➂ : Magnetic flux leakage causing winding vibration
In the case of non-shielded power inductors without a shield core, vibration caused by the magnetization of the aforementioned core and shield ring will not result in whistling, but other problems will arise in non-shielded products. Due to the open magnetic circuit structure of non-shielded products, leakage flux often affects the winding. According to Fleming's left-hand rule, force acts on the winding because the winding carries a current. Therefore, when an AC current flows through the winding, the winding itself vibrates, producing whistling (as shown in Figure 5).
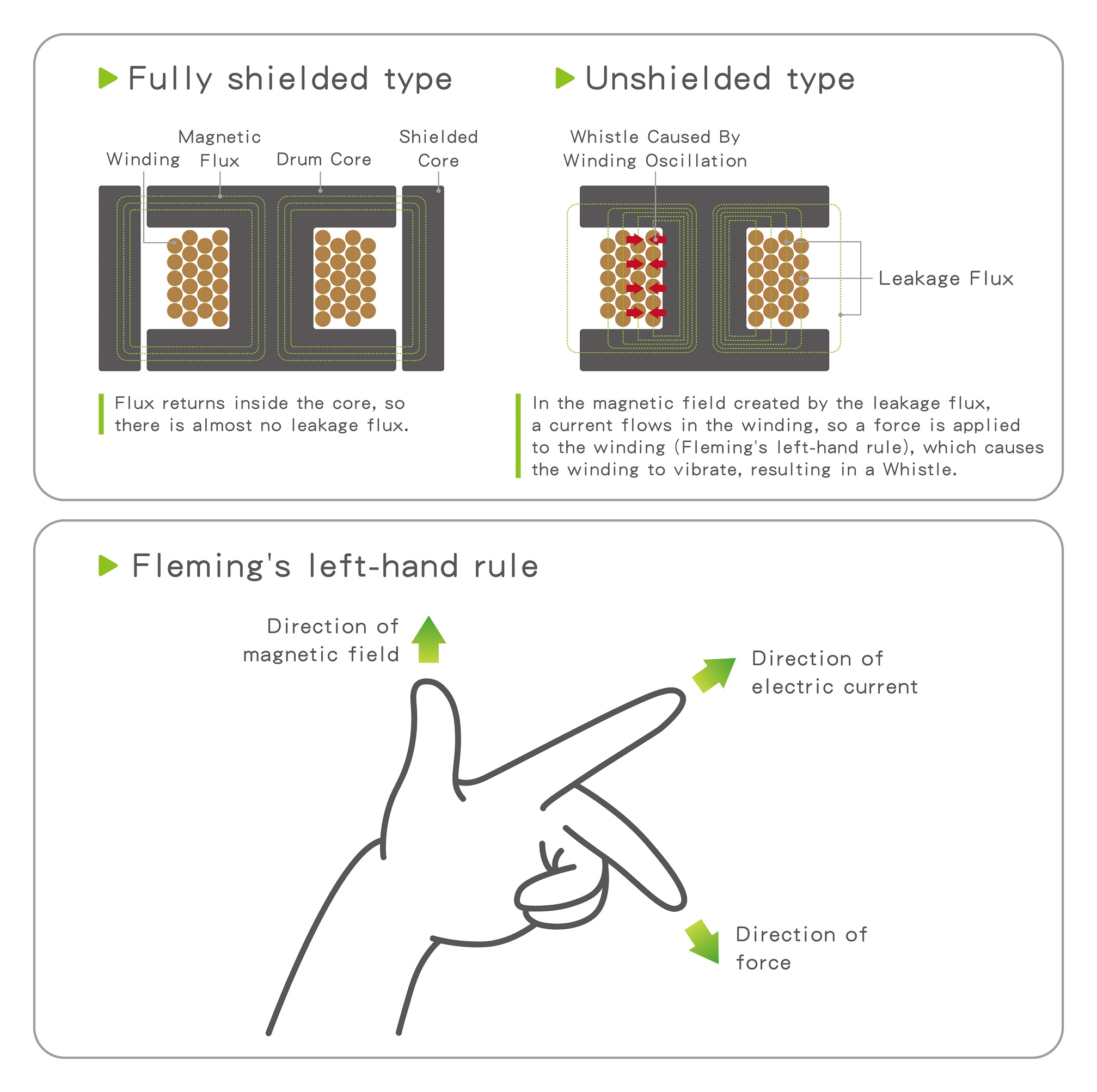
Figure 5: Flux causes winding vibration
4. Various causes of noise amplification
➀In power circuit boards with high-density installation of multiple electronic components and devices in contact with other components, the subtle vibrations of the inductor will be amplified, resulting in audible whistling.
➁ Leakage flux causing effect on surrounding ferrite
When there is a shield or other ferrite around the inductor, the ferrite will vibrate due to inductance leakage, resulting in whistling.
➂ Consistent with the overall inherent vibration of the assembly including the substrate
Generally, in products such as inductors, small ferrite cores are used, and their vibration caused by magnetostriction is not considered noise since it is consistent with the inherent vibration of the components, including substrates. However, when the inductor is composed of multiple components and mounted on a substrate, multiple inherent vibration frequencies within the range of human hearing can be generated, and the resulting vibration amplification can produce noise. Additionally, if the vibration frequency is consistent with multiple inherent vibration frequencies of the entire component, it may cause a whistling sound after being installed into the device.
5. 4 solutions to power inductor noise.
• The following are four solutions to the noise of power inductors in DC-DC converters.
• Key point 1: Prevent the flow of audible frequency current through the human ear
The most basic countermeasure is to prevent the flow of audible current through the human ear. However, in the case of DC-DC converters with intermittent operation and frequency-variable modes aimed at energy-saving, where it is difficult to prevent audible current from flowing, the following noise reduction solutions should be attempted.
• Key point 2: No ferrite placed around
If not placed around the inductor, the ferrite (shield, etc.) may be affected by leakage flux. When it must be placed nearby, choose a shielded inductor with less leakage flux (closed magnetic circuit structure) and pay attention to the placement direction.
For example, use GOTREND GSTC、GSTM-Series one-piece molded inductors, you can have the best shielding effect
.jpg)
• Key point 3: Misalignment of natural resonant frequencies
Sometimes, it is possible to reduce whistling noise by misaligning or increasing the natural resonant frequencies. For example, changing the shape, type, layout, or tightening the substrate of an inductor can alter the overall natural resonant frequencies of the components on the substrate. In addition, noise is often common in high-power inductors over 7mm. Natural resonant frequencies can be increased by using low-power inductors below 5mm, thereby reducing whistling noise.
• Key point 4: Replace with integral molding inductor
As mentioned above, in fully shielded power inductors, the bobbin and shield magnetic core will attract each other due to magnetism, but it will cause whistling at the gap position (e.g. GOTREND GSBS series
). In unshielded power inductors (e.g. GOTREND GSDR series
), wire vibration caused by leakage flux will lead to whistling.
Replacing with integrated inductors is a useful solution to the noise problem of power inductors (e.g. GOTREND GSTM series). This is achieved by integrating the hollow coil into a soft magnetic metal powder for one-piece molding. Due to the absence of gaps, the magnetic cores will not attract each other, and at the same time, the winding resistance vibration problem caused by magnetic flux can be avoided by integrating the coil with the ferrite.
In addition, GOTREND's products use a metal magnetic material with less magnetostriction, so vibrations caused by magnetostriction can be suppressed. From the perspective of magnetic components, whistling noise can be reduced by replacing unshielded or fully shielded traditional assembly choke.
Comparison of noise between fully shielded and integrated power inductors:
A microphone was installed in a soundproof box, and a sinusoidal current ranging from 0A to the rated voltage was applied to the measurement samples mounted on the substrate for 60 seconds. The peak sound pressure was recorded by sweeping frequencies from 20Hz to 20kHz, which are audible to the human ear. Install the microphone in the sound attenuation box, use a sine wave current of 0A to rated voltage to power on the measurement sample installed on the substrate for 60 seconds, and scan at a human ear audible frequency of 20Hz to 20kHz to record its peak sound pressure.
The analysis and comparison of noise generation were carried out using a fully shielded assembly inductor (GOTREND GSBS series, approximately 12x12x6 mm) and its integrated power inductor (GOTREND GSTM series, approximately 12x12x6mm) as measurement samples.
As shown in the figure below, when comparing two different types of inductors, it can be observed that sound pressure levels vary with frequency.
• Traditional Assembly inductor :
Noise of about 30~50dB is generated in a wide frequency band.
• Molding inductor :
In the category frequency range, it is at the same low level as the background noise, and even at the peak position, it suppresses approximately 18dB more than the fully shielded assembled inductor. A suppression of 18dB means only one-tenth of the level, indicating that replacing with a molding inductor is an effective method.
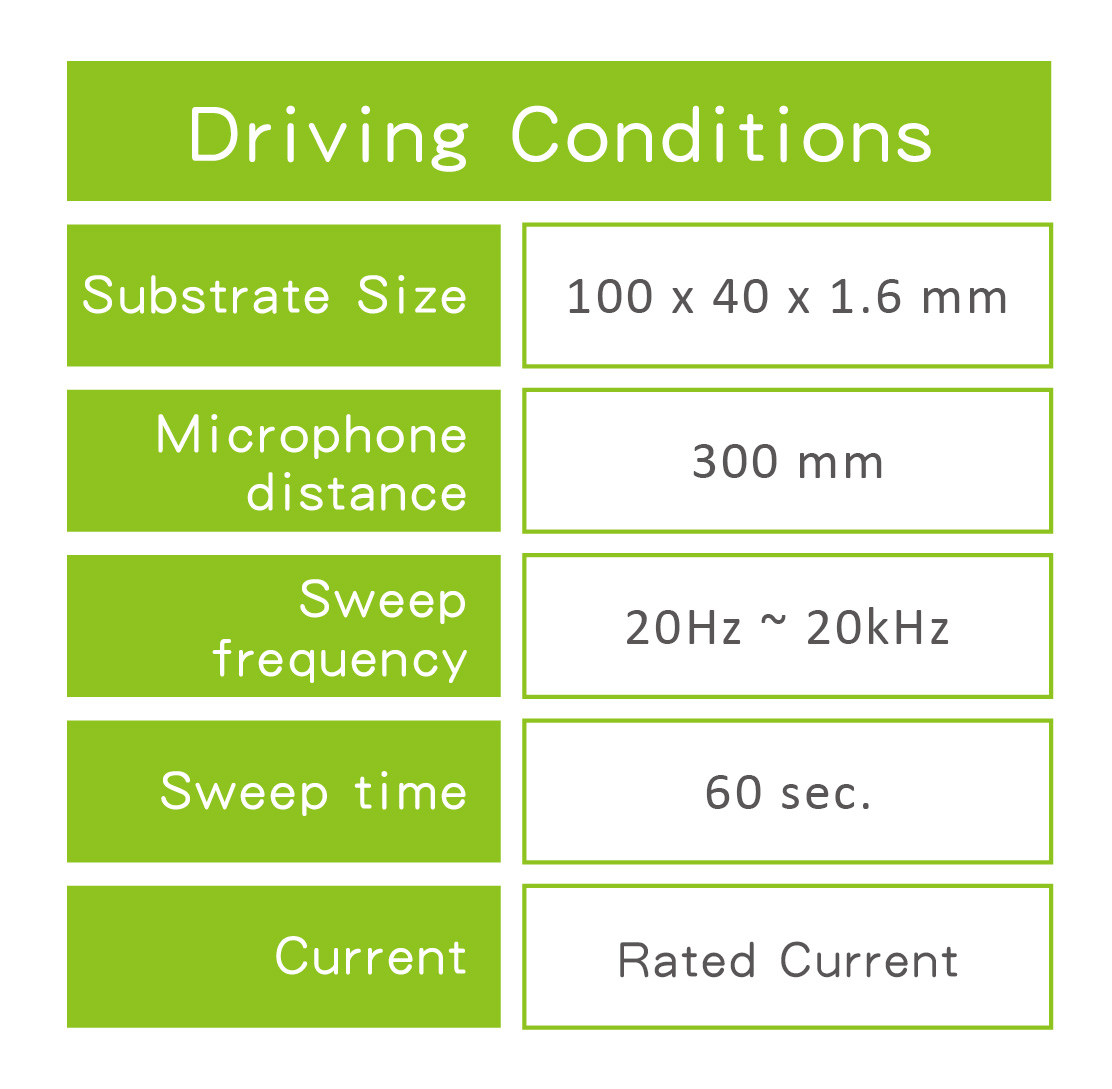
Figure 6: Example of noise assessment for various types of power inductors
If you are interested in our products, please Contact Us.